The Pitmans Parliament Refurb
Durham Miners’ Association New Hall and Offices, affectionately known as Redhills, stands as a testament to the rich history of social progress and community enterprise in North East England and we have been delighted to be involved in the major renovation that is has gone through.
It initially opened in 1915 to replace the former Miners’ Hall building in North Road. From the Industrial Revolution to the 1960s, coal mining played a crucial role in the UK’s economy, employing hundreds of thousands of men and producing millions of tons of coal annually. The hardships faced by miners and their families paved the way for a movement of social reform, which predated the welfare state and left a lasting impact on society. Redhills, situated in Durham’s city centre, is a Grade II listed building and home to the Pitman’s Parliament, representing one of Europe’s finest examples of trade union architecture.
At the heart of Redhills is the Pitman’s Parliament, a unique assembly that provided a platform for miners to voice their concerns and shape the future of their industry. This democratic institution allowed miners to debate and pass resolutions on various issues, from pay and working conditions to broader social and political matters. The Pitman’s Parliament was a powerful symbol of working-class empowerment and was crucial in shaping the region’s social and political landscape.
As part of the full renovation the central section of the existing Parliament floor was to be removed with a whole new floor structure introduced. We were introduced to the project in November 2023 and asked to provide a quotation for Lewis Deck and we received the order, totalling 130m2, for the project in June 2024.
The Lewis Deck was collected from our warehouse a couple of days later and the installation was completed in just a few days.
Triangle House, West Sussex.
It isn’t very often that you get involved in something truly off the wall and out there. With this new timber framed “triangle” shaped house in West Sussex we certainly had that.
Due to the shape of the site, the proximity of a railway line to the rear of the property, and not to mention the main sewer line that runs through the site the new house was designed to be triangular, not just in plan but also the walls and roof. Luckily the person taking on this stunning project was up to the task.
Done as a true self-build the timber frame was built in just a few weeks meaning that we were able to supply the Lewis Deck only 6 weeks from starting on site.
In total we supplied 120m2 of deck, which were then laid on the top 2 floors of the house, along with both of our flanking and rubber resilient strips to maximise the acoustic performance through the two floor zones.
With no straight-walled rooms and a dramatic sloping zinc roof that touches the ground on one side, their eye-catching home was featured on the Channel Four programme Grand Designs where presenter Kevin McCloud described it as one of the trickiest plots ever seen on the show and the resulting home as a ‘giant 3D geometrical puzzle.’
FastSlab Renovation Project, Hampshire
This project in Hampshire was a pair of semi-detached houses that were getting the full refurb treatment. The ground floors were suspended timber floors that were old and damaged. It was decided that the best plan was to remove the old floors and replace them with a much better and stronger system that wasn’t going to degrade over the coming years.
Initially we were contacted back in March of 2020 regarding our FastSlab Ground Floor Renovation system and we made delivery of the system in June. Below you can see a number of photographs from the project detailing the installation.
Once the old floor was removed a central sleeper wall was installed to reduce the spans of the FastSlab joists and a steel angle was installed to support the joists as the new system works on either 900mm centres, or as in this project, 600mm centres. The old timber joists were installed at 400mm centres so it isn’t possible to use the old joist positions.
Once the angle was installed the installation of the main floor can commence. This is relatively straight forward as there are only 3 elements to it. The steel joists, the insulation blocks and the Lewis Deck dovetailed sheets to create the base for the screed floor.
As you can see from the photo below the insulation blocks wrap under the steel joists to stop cold bridging from occurring. This is where cold can travel through the system and up into the room above.
The joists are 180mm in depth and come in lengths from 3.0m to 5m. The joists in this project were 3.6m in length and they were installed at 600mm centres.
Adding a Floor to an Existing Building
One of the great things about Lewis Deck is its versatility when it comes to the type of building it can be installed in. This one is no exception. Here we see Lewis Deck being used to add a floor on top of an existing building in London.
Lewis Deck was chosen, on this particular project, for a number of the key benefits the system brings. These being the strength of the system with only needing a thin screed on top, the acoustic qualities & vibration control properties and the speed an ease of installation.
This project even requested much longer sheets than standard in an effort to speed up the installation process even more. In fact you can see from the main photo above that some of the sheets were extremely long. The longest being just over 6.5m.
We initially started work on the design side of this project back in 2016 and after a 2 year gap we were brought back on board in 2018 to continue the discussions regarding the deck. The order was eventually placed in early 2020 and after a delay due to the site closing down during the lockdown period we eventually delivered all of the deck in August this year.
The deck was laid on top of a steel beam/ joist structure and fixed down periodically. The joists were installed, mainly, at 400mm centres and the deck was cut to size to match these centres.
AVRO, Manchester. Listed Mill Building.
It’s not everyday you get a phone call from an architect asking for help on a grade 2 listed mill building, but that is what happened to us back in April 2017 when Stephenson Studios contacted us with a problem they were having with floor to ceiling heights on their Brownsfield Mill project in Manchester.
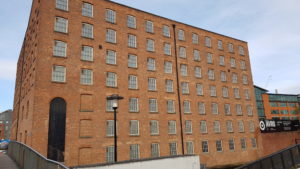
Their design criteria was for the existing 75mm thick timber mill boards to be retained and each of the apartments in the building would have these as an exposed ceiling. The idea was to keep the building as rustic and to retain as much of the original look and feel of the listed mill building as possible. Because of this all of the acoustic (Part E.) and fire Building Regs. (Part B.) requirements would have to be installed above the existing floor.
The drawings we were sent through identified a floor build up, on top of the mill boards, at nearly 300mm thick. This started with a self levelling compound on top of the mill boards, to level them to, and then a timber on timber solution with a final layer of cement particle board prior to the oak flooring being installed.
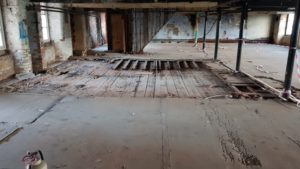
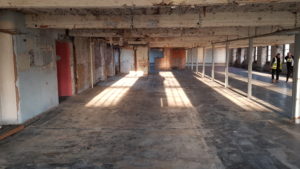
This thick floor section was causing a problem due to the original oak beams that were in place meaning the floor to ceiling heights weren’t as high as they needed to be. This design was compounded flowing the removal of the bitumen floor covering. When the mill boards were exposed and then levels were taken across each of the floors it was clear that the original design was no longer suitable for the project.
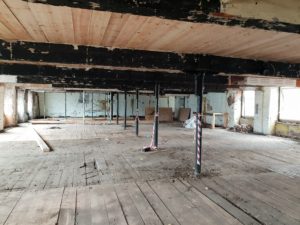
With the age of the building some of the mill boards were beyond repair and each of the floors needed levelling up so the use of self levelling compound and a timber/ cement board solution also became a very expensive solution. We were asked if we could come up with a solution that was able to reduce costs and time and also to be able to achieve the required acoustic and fire requirements for this type of conversion project.
Our initial thoughts on the project was to use timber ferrings, 100mm wide at 600mm centres, to lay our Lewis Deck system onto. This was reducing the number of ferrings by 50% (these were originally at 400mm centres) and it also removed 4 layers of timber/ cement board as well as the self levelling compound from the project. Following a meeting on site however, and after being able to fully talk to the deisgn team and developer about what the Lewis Deck system can do we agreed that we would look at putting the ferring strips at 1400mm centres with the Lewis Deck being laid across at these centres. Rubber granulate acoustic strips would be installed on top of each of the timbers and mineral wool insulation would then be installed between. This would allow more material to be removed from the project but crutially still hit both the acoustic and fire requirements of the project.
A test floor was commissioned, by the acoustic engineer, and built in August 2018 which passed all tests. You can see from the photos below the Lewis Deck laid at 1400mm centres for the middle section of the test with the 15mm thick rubber granulate acoustic strip laid on top of the timber ferrings. These timbers, due to the nature of the mill boards below, had to be installed individually to differing heights.
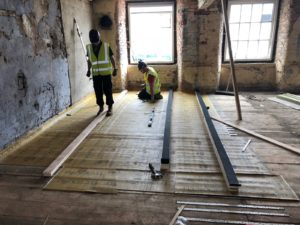
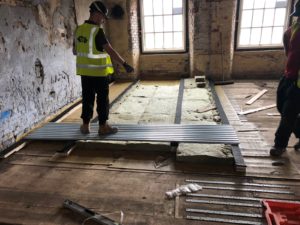
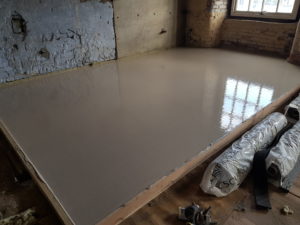
Urban Splash Website – AVRO/ Brownsfield Mill
Continue reading to find out how the installation element of the grade 2 listed mill building project went.
Timber Frame Self Build, St. Albans
It is always nice to get an invitation down to a project that we have supplied our Lewis Deck to and this timber frame self build is a great example. It’s especially nice when we get to visit people and contractors who are using Lewis Deck for the 1st time and this project was just that.
Situated just outside of St. Albans we visited the project on the 1st Wednesday back after the Christmas break. Luckily both the weather and the traffic were fine so there were no issues getting there.
We were asked to visit site as the screed pour was planned for the following day and they wanted to make sure that everything was ok, from our point of view, prior to the screeders arriving.
A quick note on the design of the floor in this type of project. A timber frame structure, in the majority of cases, requires the floor to provide what’s called racking to prevent the building from twisting over the course of the life of it (this isn’t required for other build systems). This means that the floor needs to be secured to the joists below so that the floor can stop this twisting. Now because we generally recommend that Lewis Deck is laid as a floating floor meaning you get much better acoustic figures through the floor there are a couple of ways of creating this racking within the timber framed floor. Firstly is to fix the Lewis Deck down and take the hit with the acoustic performance or the second way, and most popular, is to introduce a timber deck fixed on top of the timber joists with the Lewis Deck then laid loose on top of the timber with the resilient acoustic strips acting as the sandwich filler in between. In this build up you keep all of the benefits Lewis Deck gives you but it is a slightly deeper floor section as you add in the 15mm timber deck (this thickness is specified by the timber frame manufacturer and not by CDI).
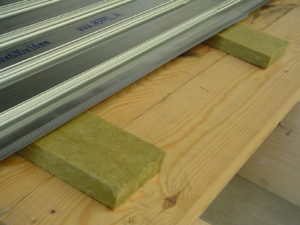
Insworke Mill Quay
Insworke Tidal Mill was originally built around the 1590’s and survived as a working Mill until just before the First World War.
It then had a chequered life as various storage and manufacturing uses until it fell into total disrepair. It went under a major refurbishment and rebuild programme in 2011 to find a new life as a commercial property to the ground floor and residential to the upper floor.
The client turned to a Lewis Deck / screed solution when looking for solve the problem of acoustic and fire separating floors that would allow the new timber beams to be left exposed from beneath to replicate the original beams. On the ground floor Lewis was used to in a similar way to create a warm floor above the voided cellar areas. Lewis Deck on resilient strips was placed on to the new beams with a flanking strip around the perimeter. Underfloor heating was then fixed to the Lewis Deck before the screed was laid giving an overall depth of deck, underfloor heating pipes and screed of just 52mm.
The system is often used in this way in listed buildings such as this to preserve the existing structure and upgrade the performance of the floor. As the floor is laid as a floating structure, that is, without connecting it to the existing timber, it doesn’t damage it and if required, could be removed in the future to bring the floor back to its original state.
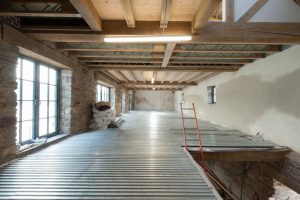
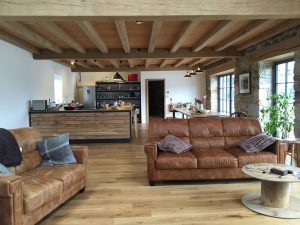